beal collection
Our limited edition Beal collection is woven using very fine South Island grown Merino wool, in a variety of colour ways. The unconventional herringbone pattern of these scarves reference the tradition and strength of herringbone, within a contemporary design.
Beauty, luxury and wearability ... the Beal collection.
shop our
beal collection
Available
Online
Crafted: Waitaki Artisan Gallery in Oamaru.
Olveston Historic Homestead in Dunedin
At McLean & Co we are passionate about preserving traditional textile skills and designs and using the finest New Zealand yarn and bringing them into today's world, as you can see in the contemporary twist we've added to the traditional herringbone design of our Beal collection.
The Beal collection was woven by Rod on our Mark 1 Hattersley dobby loom, the only one left working in the world.
Like all our collections, the Beal collection is named after a street in Oamaru. Beal Street was named by Surveyor Thompson for the River Beal, a small river in Greater Manchester, England.
weaving the beal collection
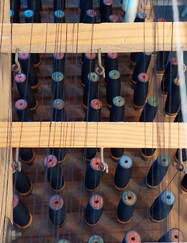
This was a tricky and time consuming warp to make. Due to the style of our warping frame, we can only have a maximum of 150 bobbins for each section of the warp. At 36 ends per inch each four inches has 144 fine Merino ends.
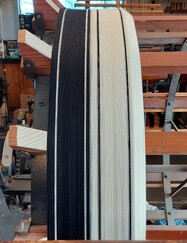
This meant that all the black with little white stripes was wound onto the mill first. Then all those bobbins were taken off the frame and the white with little black stripes was put on. All by hand, patiently, in the correct order.
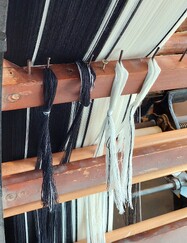
Looking at the inside of the warping mill you can see the individual sections as they are fastened on, wound on and fastened off.
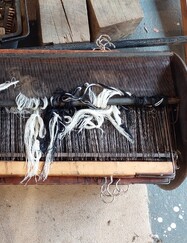
Every thread is threaded and pulled through the reed on the beater, and now everything is ready to be carried over to the loom and installed. This can be a very tricky manover as there are a lot of components to get safely on the loom, and lots of things to go wrong.
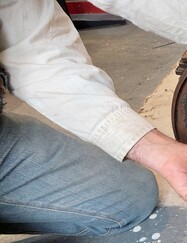
The weaver, tightening the brake drum on the back beam. The brake drum puts resistance onto the warp to keep everything at an even tension.
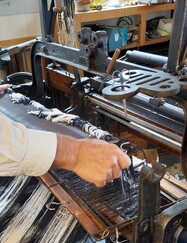
Working steadily, and thoughtfully. If things slip now it would be a nightmare to fix. When Rod saw this comment he said, "Well, that's an understatement!"
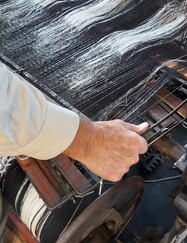
And the back beam is in place. Now the shafts have to be aligned and hooked up to the dobby mechanism, without the threads pulling back through the reed or the leading shafts.
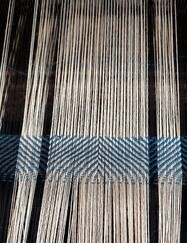
The first few rows of weaving are always a bit nerve wracking. This is when we check that we've threaded everything up correctly, and that Rod has tuned the loom so that everything is tensioned and posititioned correctly, ready to weave 70 metres of Beal fabric.
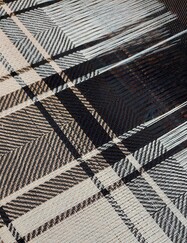
Weaving is underway. Each weft thread equates to one pedal of Rod's leg. If he's not pedalling, he's not weaving.
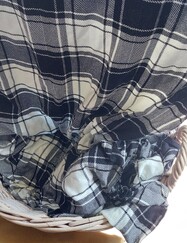
After fulling the fabric and rinsing it in our washing machine, it's ready for Rod to gently stretch it onto our drying roller, that hangs from the ceiling in our lounge.

This is a really important part of the process. The warp and weft threads need to line up at right angles to each other or the fabric will dry crooked. In fabric finishing factories they have tentering frames where the fabric is stretched and set into its final dimensions. We don't have one, and there is nowhere in NZ for us to send our fabrics to be finished, so we do it ourselves, in a Kiwi number eight wire way.
CARE INSTRUCTIONS
Please handle this fine Merino wool scarf with care. Avoid snagging. We recommend washing
gently by hand using an eco-friendly wool wash. Dry flat in the shade. Cool iron.
DO NOT MACHINE WASH OR TUMBLE DRY.