Meagan, from Meadowslea farm, near Fairlie, first approached us early in 2022, asking if we could weave some of her wool into curtain fabric. It was the beginning of quite a long process, involving people skilled in their part of the wool production sector. We call this slow production! Meagan has been involved in every step of the process.
Firstly the sheep were shorn. Two bales of the 2022 wool clip were sent to Timaru for scouring, then to Wild Earth Yarns in Christchurch to be spun into yarn suitable for weaving curtain fabric. We received the yarn, in the first week of May 2023. Rod finished weaving the first 150 metres of fabric in July.
Meagan will have fabric for sale later this year, once we have woven more for her. If you would like to buy of this very special fabric some please contact me at hello@mcleanandco.nz and I will give Meagan your contact details.
"Meadowslea Romney stud, founded in the 1920's, is located on the picturesque foothills of Fairlie, South Canterbury. It has long held a reputation for quality sheep who thrive in the hill country and to do this it is essential that they wear a good fleece. The strong crossbred wool they grow is ideal for fabric manufacture.
The idea for curtains came to me while handling the ram hogget fleeces at shearing time. Each fleece is individually weighed and micron tested as part of Meadowslea's ongoing commitment to breed high quality wool. We were excited to come up with a way to utilise the beautiful natural fibre in our home. What a lovely view we will have every time the curtains are drawn."
Meagan McLeod
The process ... from farm to fabric.
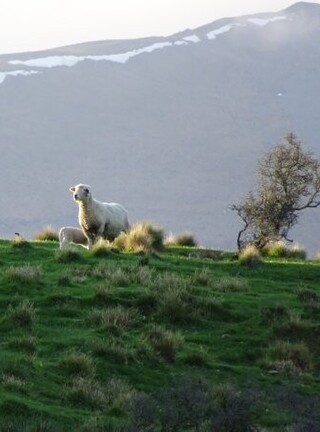
Meadowslea Romney stud, founded in the 1920's, is located on the picturesque foothills of Fairlie, South Canterbury. It has long held a reputation for quality sheep who thrive in the hill country and to do this it is essential that they wear a good fleece. The strong crossbred wool they grow is ideal for fabric manufacture.
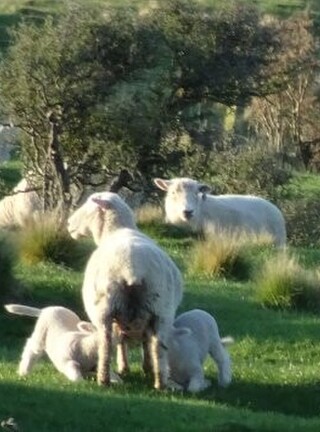
Romneys have been bred at Meadowslea since 1926, and have had generations of selection for structure, bone and constitution. For the last two decades they have lambed totally unshepherded, resulting in-built survival that sets Meadowlea's sheep apart.
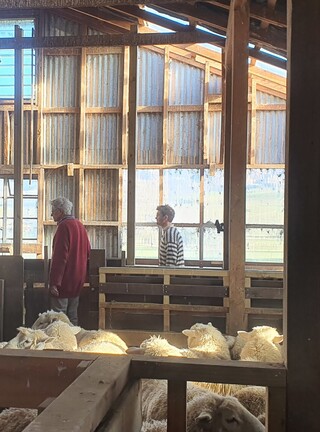
A view inside the shearing shed at Meadowslea. These are the sheep the wool for Meagan's weaving came from. It is really special to know exactly which sheep have provided the fleece for the fabric to be woven.
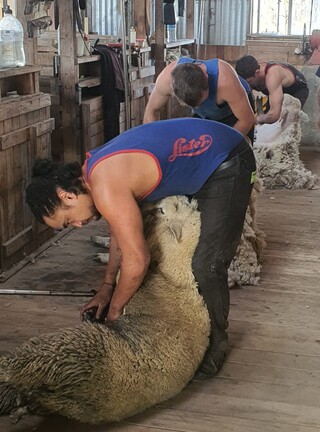
Shearing in action. Shearing is a specialized skill. It is hard work. Shearing requires skill so that sheep are shorn efficiently without cuts or injuries to the sheep and shearer.
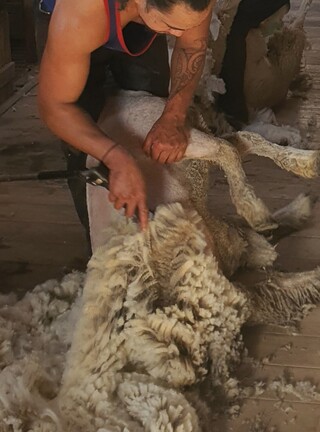
When it comes to the art of shearing, it is preferable to get the fleece off all off in one piece. It makes for a much easier job when sorting, as different parts of the fleece are used for different products e.g. clothing, carpets, blankets etc
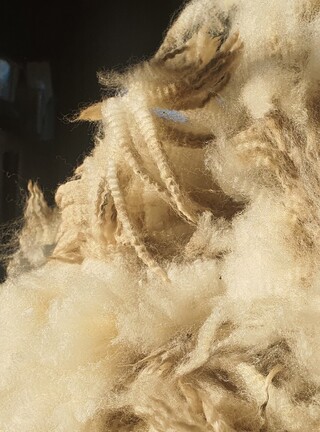
Wool has a natural waviness called “crimp.” This crimp contributes to wool's insulative properties, which exist because the bulkiness of wool naturally traps air. Some types of wool have more crimp than others. Romney has less crimp than Merino as it is a stronger, more coarse fibre, great for durability.
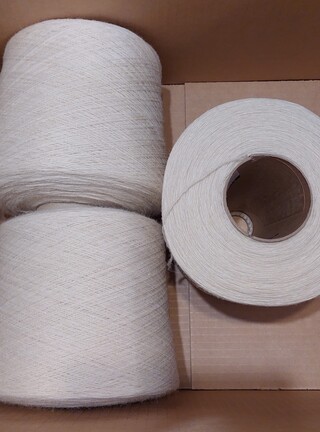
We received the 120 tex woollen spun yarn from Wild Earth Yarns on 4 May 2023. It comes on cones, ready for us to transfer to the wooden bobbins that fit on our warping frame.
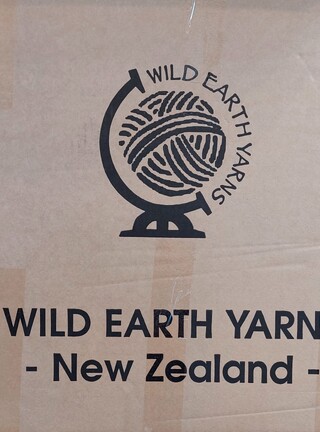
We have woven quite a lot of yarn spun by Jacqui and Graham at Wild Earth Yarns in Christchurch. Click HERE to visit their website.

Rod is putting in the cross, creating a division between under and over threads, to make it easier to thread the heddles with the herringbone design Meagan has requested.
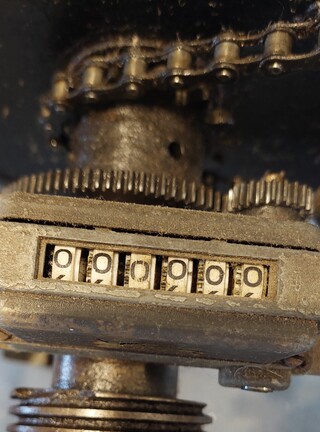
The counter - each four inch warp length has to be the same length. In this case the counter has to read 470. Rod has to keep an eye on the numbers clicking over - otherwise the warp ends will be of different lengths and make it very difficult and time consuming to finish the warping process.
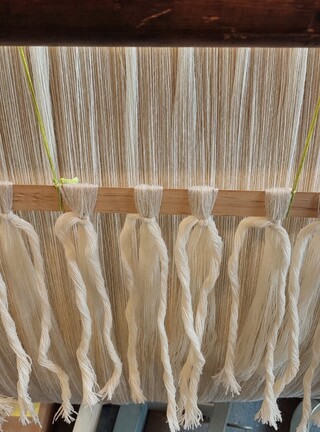
I included this image just because I love the way you can see the rawness of the yarn, and the potential of what is to come.
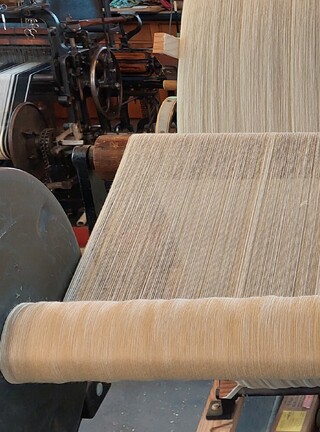
Beaming the warp ... Rod turns the handle that winds the back beam, which draws the warp yarn off the mill and onto the beam.
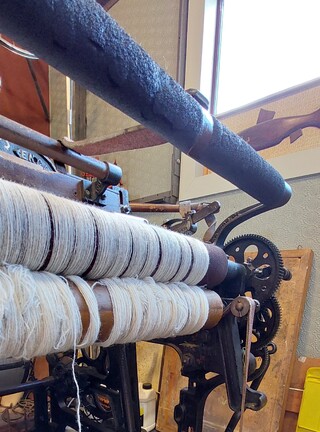
And magically (joke) the back beam, shafts and beater with the reed enclosed are on the loom. I was helping and forgot to take photos. It's quite a mission, especially with a long warp on the back beam, to get everything carried over and installed. It takes patience and the need to follow each step correctly, otherwise everything turns to chaos.
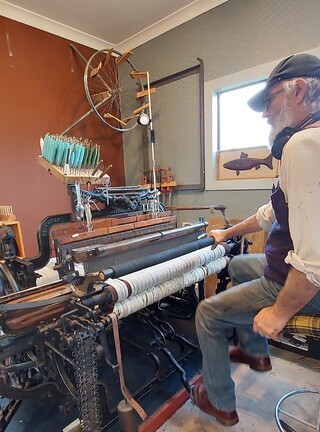
Here Rod is beginning the loom tuning process. Every new warp means retuning the loom, as each warp we weave uses different yarn to the one before.
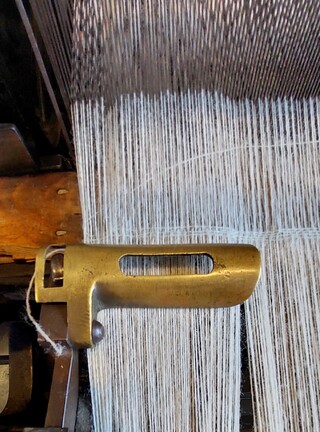
The brass temple which will grip the fabric, keeping the selvedges straight and even. Without the temples the fabric is likely to gradually get more and more narrow as the shuttle shoots back and forth.
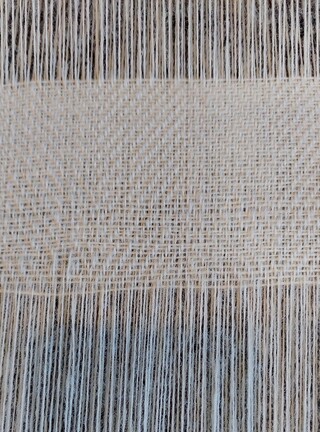
The first couple of inches, and it's looking like we threaded up the pattern correctly - that's always a relief. This coarse woollen spun yarn is causing a few headaches for Rod as it's quite hairy, causing the warp threads to catch on each other. Rod has to patiently work through each stage of the tuning process.
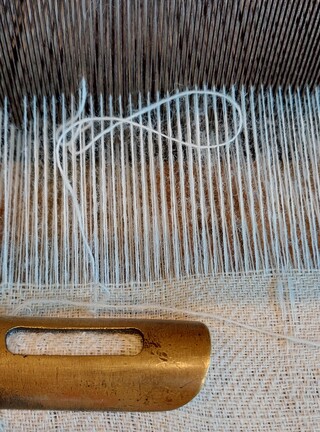
Broken threads are quite common at this stage. They are frustrating and time consuming to fix, but just part of it.
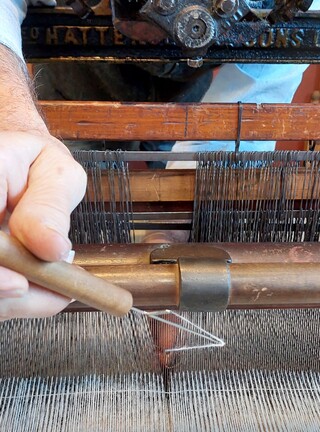
Rod using his wee hook gadget to pull the replacement thread through the empty heddle and the right dent on the reed.
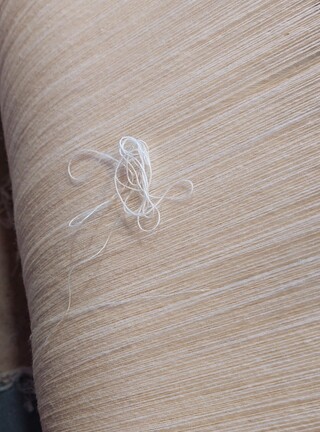
A broken thread sitting on the back beam waiting until it's long enough to be threaded back through its heddle and the reed to continue weaving.
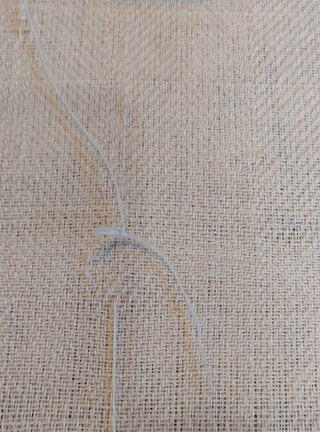
A repaired thread. You can see how it has been woven it. The ends will then be trimmed and the mend will be invisible.
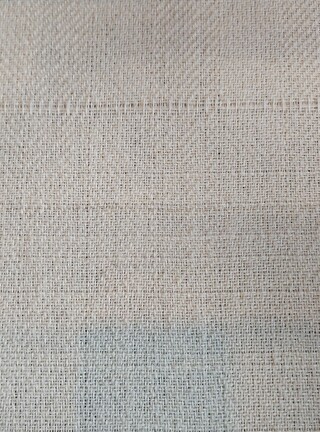
The lines across the weaving are the result of shaft #3 catching on shaft #4 as they were rising and falling. Rod fixed it by making more adjustments - all part of tuning the loom to ensure easy, even weaving.
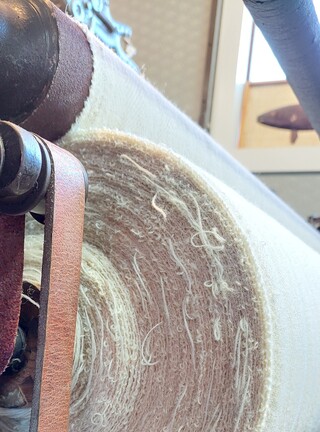
Finally, after days and days of weaving, it's time to cut the first approx 50 metres of fabric off the loom. The front beam gets too full to keep weaving. Also by cutting it off Rod can darn it and then we can full it and get it dried, measured and ready for Meagan to pick up.
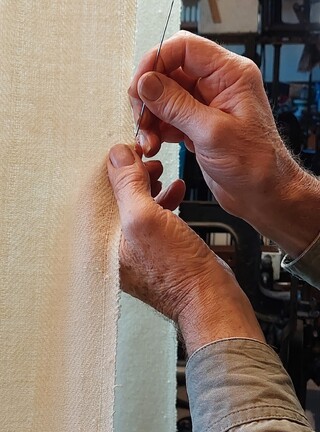
Rod, darning the fabric. I'll get more images when he's darning the next lot. It took Rod over 10 hours to darn this 50 metres due to the number of broken threads that keep happening during the weaving.
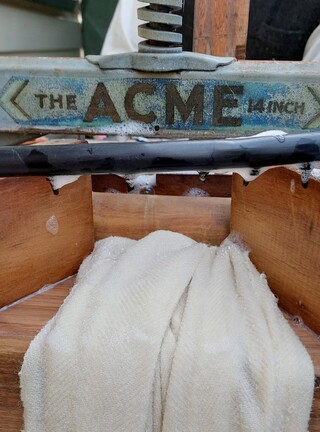
On Friday afternoon Rod set up our micro, mini, very basic fulling mill so we could make a start on Saturday morning. Because there is nowhere in New Zealand to send fabric to be finished we have to do this process by hand, under our back veranda where there is access to hot water.
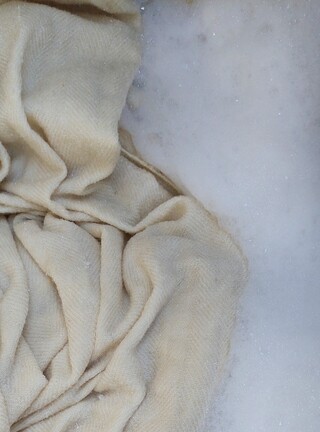
The length of fabric is immersed in hot soapy water and is fed through a mangle and back into the water - round and round it goes until we feel it has the right 'handle'. It took the both of us working together two and a half hours to full the approx 50 metres.
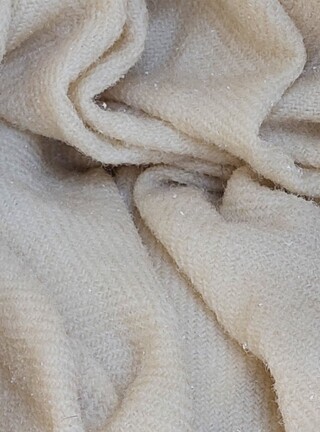
A close up of the fabric immersed in hot water. You can see the herringbone design, and the character of the woollen yarn.
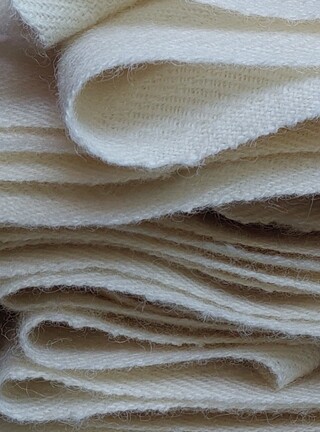
The first few metres of the 50 metres we fulled are dry. Here you can see the selvedge edge of the fabric.
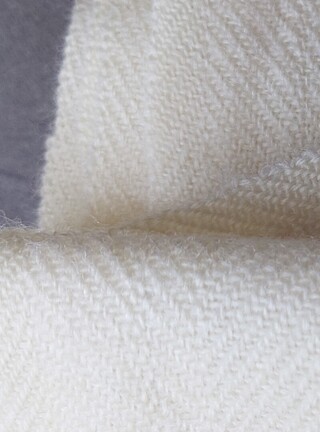
A close-up of the fulled fabric showing the herringbone design and slight fluffy texture of the woollen spun yarn.